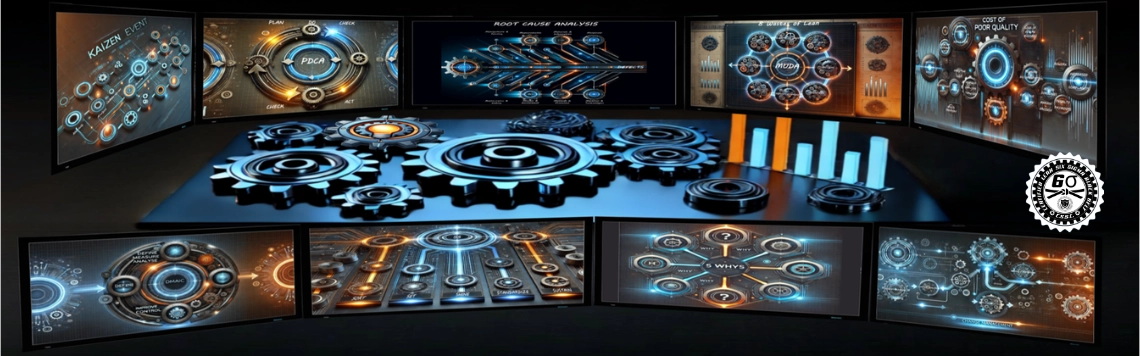
Lean Six Sigma Training (DMAIC) & Skill Development
At OpEx Innovative Designs, our Lean Six Sigma Training & Skill Development programs elevate your team’s expertise and drive significant process improvements across your organization. By integrating the Define, Measure, Analyze, Improve, and Control (DMAIC) phases into our training, we equip your team with the knowledge to identify the necessary next steps to support your continuous improvement efforts.
Tailored for both production and administrative personnel, our hands-on training ensures the consistent application of Lean principles. By blending proven methodologies with real-world applications, we empower your team to identify inefficiencies, implement effective solutions, and achieve sustainable success for immediate, measurable improvements customized to your environment.
‣ Services:
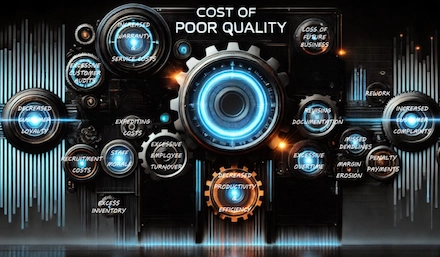
Establishing a Lean Foundation (Define)
We establish a strong Lean foundation by training teams in 5S, Change Management, Cost of Poor Quality (COPQ), and Theory of Constraints (TOC), while prioritizing KPI Development to foster continuous improvement and enhance performance through data-driven decisions.
Understanding and Tracking Performance (Measure)
We equip your team with the skills to accurately measure and monitor performance, strengthening their foundation for informed decision-making and proactive improvements.
Process Evaluation and Root Cause Training (Analyze)
We train teams in DMAIC (Define, Measure, Analyze, Improve, Control), how to identify the 8 types of waste, and apply root cause analysis techniques like the 5 Whys and Fishbone Diagrams. This systematic approach helps eliminate inefficiencies, implement targeted improvements, enhance operations, and support continuous growth.
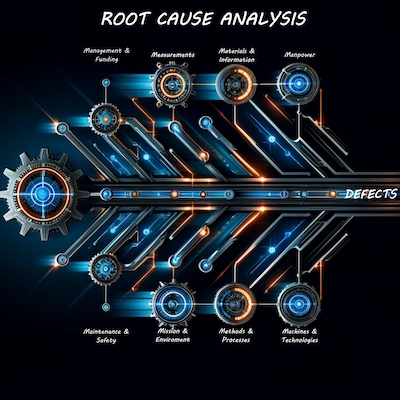
Enhancing Processes and Implementing Solutions (Improve)
Through Kaizen workshops and Poka-Yoke (mistake-proofing) techniques, we empower teams to develop and implement incremental changes that enhance process performance, boost efficiency and quality, and reduce errors and defects.
Sustaining and Scaling Improvements (Control)
We train your team to document and standardize best practices by integrating 5S, visual management, and work cell standardization into daily operations. By equipping your team with continuous improvement tools, we empower them to maintain and scale enhancements over time, fostering a culture of excellence while supporting growth through adaptable, standardized processes.