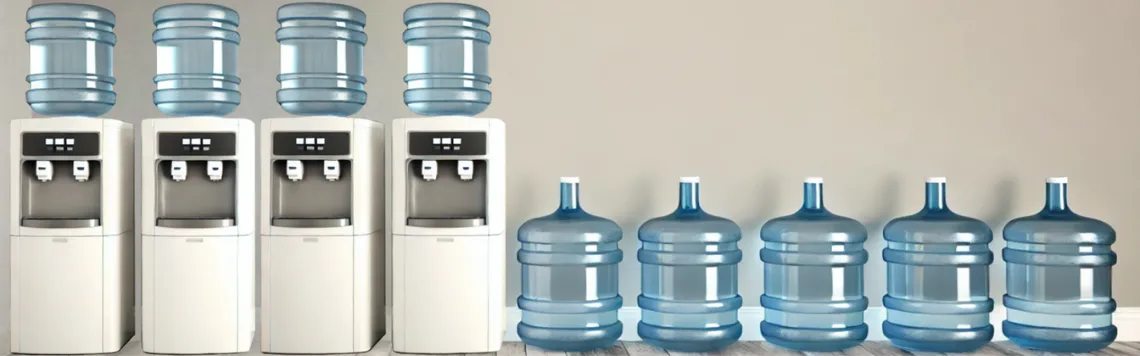
A Case Study in Process Optimization
It’s Just Water…
‣ The Challenge
An OpEx Innovative Designs’ client sought assistance to identify and eliminate wasteful practices to enhance their operations. Among several recommendations, one solution targeted their production line drinking water dispensers, which were costing $47,832 annually. Workers frequently allowed the units to run dry, burning out heating elements and necessitating an average of three replacements each month. Additionally, six water bottles were replaced daily, with each replacement taking an average of 25 minutes per station due to travel time and social interactions. Monthly deliveries occupied six large pallet rack spots, consuming valuable storage space. Insufficient sanitation practices, such as failing to wipe bottle tops prior to placement, allowed dust, germs, and other contaminants to enter the water supply.
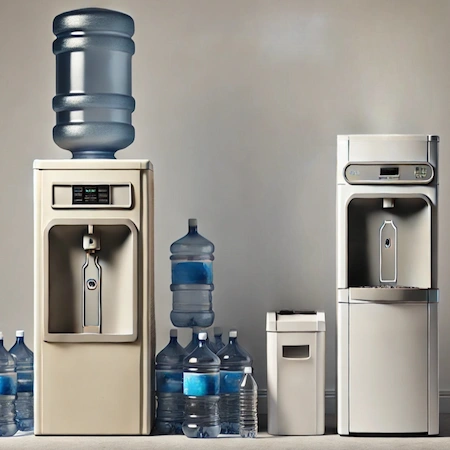
‣ The OpEx Solution
We focused on the client’s key objectives: lowering operational costs, reducing storage needs, increasing productivity, improving water quality, and ensuring scalability and sustainability without impacting production throughput.
Considering the facility’s limited water access points, unknown water quality, and the necessity to retain hot water access at drink stations, OpEx recommended the Quench Q3 Water Dispenser System. This bottle-free solution connected directly to the building’s water supply and featured advanced reverse osmosis filtration with LED-UV light to ensure water cleanliness and sanitary distribution, while maintaining access to hot water. The initial investment for installation and materials was $6,728. Additionally, there was a monthly rental fee of $648 for 24 dispensers, which included a regular maintenance package. This resulted in a total first-year cost of $13,856, with annual expenses decreasing to $7,776 in subsequent years.
‣ Transformative Outcome
The implementation of the Quench Q3 water dispensers led to substantial operational improvements and cost savings. The initial investment was recouped within just 2½ months. Annually, the client’s expenses decreased from $47,832 to $13,856, resulting in $33,976 in savings during the first year and over $40,000 in savings in subsequent years. Eliminating the need for workers to replace bottles or repair broken dispensers increased productivity and minimized distractions. Reallocating the six pallet spaces previously used for water bottle storage increased available capacity. Eliminating regular bottle deliveries and equipment replacements further enhanced long-term operational efficiency. These changes delivered a 505% ROI (return on investment) within the first year, demonstrating how a strategic investment in water management can yield significant financial and operational gains.