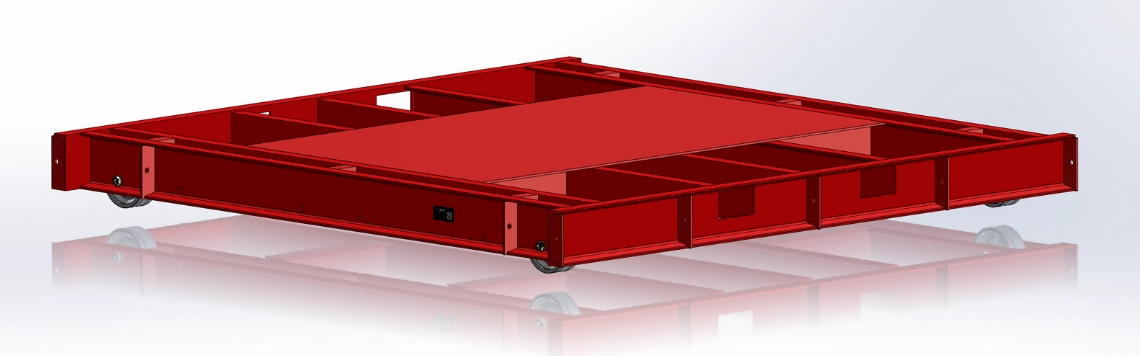
A Case Study in Tailored Equipment Solutions
Wheels Up!
‣ The Challenge
Faced with rising maintenance costs, outdated trolley designs, and frequent wheel failures, a client approached OpEx Innovative Designs to develop a smarter, more scalable solution. Their existing trolleys, which had historically handled loads of 32,000 to 40,000 lbs, were increasingly prone to expensive breakdowns and operational inefficiencies. As heavier modules were scheduled to enter production, the old design would not only exacerbate these issues but also require a significant upfront investment of $142,065 for 64 additional trolleys, plus an $5,218 per month for maintenance and an additional annual $60,002 in labor costs to move and place the modules – totaling $207,284 in the first year alone. This looming expense and operational strain prompted the client to seek a future-proof design that could handle heavier loads, reduce downtime, and curb long-term maintenance costs.
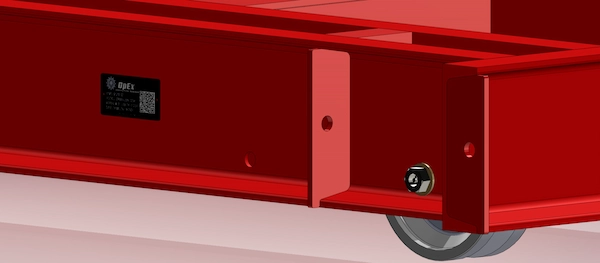
‣ The OpEx Solution
In response, we engineered a robust, universal trolley design capable of accommodating loads from 40,000 to 120,000 lbs while remaining compatible with the existing v-groove track system. Our design incorporated modular wheels for flexible load capacities of 20,000 to 60,000 lbs, forged steel wheels with grease zerk axles for in-place maintenance, and carefully optimized dimensions to ensure even weight distribution. We included forklift pockets for easier handling, powder coating for enhanced durability, and asset ID tags for streamlined maintenance tracking. At an average cost of $4,064 per unit and a total of $65,019 for 16 redesigned trolleys (including extra wheels and hardware), our approach offered a cost-effective, scalable solution that integrated seamlessly into the client’s existing facilities and multiple production lines.
‣ Transformative Outcome
The total year-one savings from choosing the re-design over the existing design was $136,483 due to reduced maintenance, downtime, and production delays. While each new trolley was about 83% more expensive than the old design’s trolleys on a unit-cost basis, the client required far fewer trolleys, reducing the total capital expenditure from $142,065 to $65,019. The re-design’s more durable components cut staffing needs by 50% for transport and maintenance and by 25% for placement, significantly boosting labor efficiency. The introduction of forged steel wheels, powder-coated frames, upgraded hardware, and asset ID tags not only extended the trolley’s service life but also laid the groundwork for future scalability, ultimately prompting the client to adopt these enhanced wheels across their entire operation. Delivering a 210% ROI in the first year, this solution ensured long-term efficiency, cost-effectiveness, and growth potential.